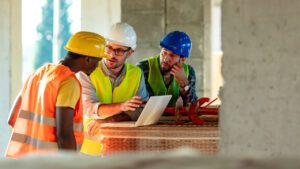
Managing with Jobsite Data
Case Study: Using Jobsite Data during Execution & After
We’ll finish this series not with more theory, but practice. What follows is a real life case study, a how-to for using real time jobsite attendance data on a high risk, time critical tenant improvement project. Here’s the setup:
Our GC is a medium size firm in an urban metro area who decided to bid on a large, multi-floor tenant improvement project for a large, high-visibility project owner. Executed right, the project would make good profits and be a showcase for further sales. But the project was high risk: The schedule would be extremely tight especially given labor and material shortages.
Further, the GC had to bid even though design was incomplete, which meant change order and t&m tracking was more important than ever. Project accounting and cash flow during execution would be tight, since wage and material inflation was peaking. Finally, the onsite crews would be three times average size, with three times the daily expense rate.
Still, management believed the risks could be managed using the digital investments they made in the prior five years:
- Microsoft Office 365 and Teams collaboration — Everyone uses the same document and messaging platform.
- Updated bid management and project accounting software — Track $$ pre-build and during execution.
- Procore cloud-hosted project management — Project and materials tasks, resources and schedule.
- Digital Jobsite Check In from Safe Site Check In — Who as onsite and why data.
Well Begun is Half Done
Our GC won the bid, lined up their subs, and, most important, documented the project’s risks. Like myself, this GC believes “risk management is project management practiced by grown-ups.” Management made sure everyone knew their role in managing those risks. One group of risk management techniques was close supervision of workers as they performed their tasks. The other was to collect the data necessary to sense and act on immediate problems, but also to avoid problems downstream.
The GC’s managers asked themselves: What data would we need if something goes wrong? Examples:
- What if the final design conflicts with our bidding assumptions?
- What if seasonal flu, colds or Covid are making our workers sick?
- What if a sub is not performing or staffing adequately?
- What if a schedule extension is justified?
- What if an accident or incident occurs?
- What if an inspection is delayed or finds flaws?
- etc.
In almost every case, the data required to mitigate risk includes jobsite check in data: who was on the jobsite, when, why and for how long. So management made special efforts to be sure all their digital tools were at launch used to the max. Initial project tasks are always on the critical path, and if they slip, every downstream tasks slips. And as downstream tasks fan out into subcontractor swim lanes, a project can quickly eat up all slack, with fewer and fewer opportunities for making up time. And if problems showed up later, even after owner occupation, they’d have the data to assure payment.
Using Jobsite Check In Data to Manage Employees
Using digital check in technology frees up supervisors to focus on managing the workers doing the building. Most supervisors do not want to be in charge of routine recordkeeping. Nor do they want to employ field engineers to input data that can be collected automatically. Digital check ins mitigated worker performance risk on the project by allowing supervisors to use their expertise on their most important duties.
All construction jobs except the most trivial need a daily log and permanent recordkeeping for compliance and dispute resolution. Our GC began using digital check ins on all its jobs during the Covid pandemic to meet state and local regulations, but kept the technology because it just made business sense. Safe Site Check In estimates a savings of $2.50 per check in across all types of projects.
Using Jobsite Check In Data to Manage Subcontractors
Key to our GC’s bid was the performance of key subcontractors, particularly HVAC and metal work. The project manager needed to be on top of all subcontractor performance daily. Did they show up? Did they adequately staff? Are their personnel performing? Because project cash flow was an issue, subcontractor payables required close scrutiny. Also, some individual trade persons charged by the hour. Check in data was used to assure they were on the jobsite as expected and putting in the hours, but also to validate timecard charges in the data looked out of line.
Again, check in data was important for validating invoices and answering accounting questions without nagging supervisors who could focus on building with fewer interruptions.
Using Jobsite Check In Data to Update Procore
Because Safe Site Check In automates the daily log and integrates the data with Procore, project managers had daily updates to manpower loading. Project managers were able to observe project progress without the need to nag supervisors. Supervisors could focus on building with fewer interruptions.
Using Jobsite Check In Data to Manage Safety
While not a safety critical project requiring an onsite safety manager, our case study project still needed to confirm to the GC safety process rules. Safety on such projects is a “level of effort” activity performed by a fractional resource.
Check in data would be essential to investigating any incident, accident or justifying insurance claims, so automated recordkeeping was essential. Safe Site Check In was also used to distribute Safety Data Sheets for any hazardous materials used on the site, and to advise workers of any significant jobsite risks, such as falls.
Using Jobsite Check In Data to Manage the Project Owner
The daily check in data combined with Procore meant the project owner had full visibility during execution and could monitor progress to schedule milestones directly. The additional real time data meant the back up data for scope changes and t&m tasks was immediately available to project accountants. Digital data meant the amount of paper handling — always inefficient — was kept to a minimum. The project had many fewer payment disputes because the backup data was available compared to reliance on a supervisor’s memory.
Safe Site Check In also fully automated visitor management, advising jobsite entrants of legal requirements, such as liability waivers; safety requirements, such as PPE, and notifying supervisors of visitor arrivals. The project owners knew they were protected from liability risk, while providing the best visitor experience at low cost.
Hard Savings and Soft Savings from Risk Reduction
Hard savings were fairly easy to quantify based on direct automation benefits. Because workers identified themselves and checked in digitally, and the data automatically transmitted into Procore, there was no paper handling or data entry required in the field. HQ groups could answer most questions themselves without contacting field personnel. With a daily average of 20 workers, hard savings were about $500/day or $10,000 per month.
Soft savings were all in the risk management bucket: Supervisor time wasn’t wasted on data entry, and they could do a better job keeping crews on task. Safety and compliance recordkeeping was automatic and easily retrievable.
Who Used Check In Data on this Project and Why
Our customers report that jobsite data is used throughout the firm in all departments as shown in the table in Part 4, published last week. How did each department use Safe Site Check In’s data on our case study?
- Check-in/out data — supervisors, project managers, safety, accounting, HR, executive management, owner.
- Observations/Photos/Notes — used by workers to document jobsite conditions.
- Safety Records — used to document compliance, PPE reminders, distribute safety data sheets.
- Incident Reports — none occurred, but the data was ready if needed.
- Daily Log Reports — kept all managers informed of daily progress on all the GC’s projects.
- GPS data — not used.
- Crew Communications — notifications of jobsite changes (fall risks) affecting safety were used
- Worker Profile — not used, although our GC plans to use data on certs, licenses etc. in the future
- Subcontractor Profile — used, would be used for insurance, license and other validations in the field
- Legal/Policy/Waivers — used for visitors
- Onboarding Video — not used
A Good Outcome to Build On
The shift to digital transformation is iterative – it’s not a one and done project – and this case study proves it doesn’t need to be overwhelming. In fact, it can pay for itself on the first project, as shown above with simple math.
We all know that field personnel, whether employees or subcontractors, will resist, push back or pretend to adopt. Nobody wants to change, after all, unless there’s something in it for them. Sometimes the motivation is immediate — did the subs show up in force? Sometimes the motivation was risk management — how can we be sure we’ll be paid for scope extensions and schedule extensions?
Bottom line, what made this a jobsite management success?
Management committed and insisted that the team actually use the digital tools. It was as simple as that. Right at the start, agreement was reached with supervisors and workers that everyone would check in every day and fully utilize Procore and Microsoft Office. The entire project team was held accountable quite easily: All management needed to do was look at the check in data every day, and if it was missing, ask the supers to explain. Excuses and non-compliance disappeared quickly. “Dude, did you check in?”.
Our GC can build on this success to bid bigger and riskier jobs, a competitive advantage, all made possible by their digital investments.
Contact Us to Discuss Your Needs
David Brian Ward is a CEO and Founder of Safe Site Check In LLC, a digital jobsite management platform launched in 2020 for the Construction industry. With over 40 years of experience in the technology industry, having launched and grown several successful companies. Mr. Ward is a now a SaaS entrepreneur and innovation leader in the Construction industry.